Table of Contents
“Inductive transducer is also called as Variable Inductance transducer. When a physical quantity to be measured, such as motion, displacement, vibration, acceleration, force, speed etc. make changes in inductance properties of the sensor coil, or magnetic properties of core material or electric properties of magnetic circuits, these sensors or transducers are termed as inductive/ magnetic sensors and fall under category of inductive transducers.”
Read more for inductance from wikipedia
Mostly, the change in inductive properties as an effect of physical quantity to be measured results as change in electrical properties such as change in AC voltage (or EMF) and or AC current which can be measured directly and hence can be calibrated in terms of unit of measurement for a range. Another output form can be pulse signals in which number of pulses counted, or pulse frequency change is detected. Thus it can be used object counting application and for speed measurement. There are both types self generating and passive type of inductive transducers exist. Various inductive transducers (which are passive transducer) are shown as follows-
- Self inductance based Transducer
- Mutual inductance based Transducer
- Variable reluctance type Transducer
- Differential transformer –LVDT & RVDT
Other Self generating type inductance transducers are as follows-
- Moving Coil generator
- Electro-magnetic type
- Electro-dynamic type
- Eddy current type
Working principle of inductive transducer
Since there are several configurations possible for inductive and magnetic transducers, working principles for inductive transducer and magnetic transducers can be understood by following-
Self inductance based Transducer
Self-inductance is the property of the current-carrying coil (inductor) that opposes or resists the change of current flowing through itself. This occurs mainly due to the self-induced EMF produced in the coil itself. , the direction of the induced EMF is opposite to the applied voltage which makes current flow through coil.
From the formulas of self inductance, it is clear that self inductance is a function of number of turns of coil, reluctance, permeability and geometric factor so when a process variable make change into the following factors, it can be measured by detecting change in self inductance which can be converted into form of change in voltage across it or current passing through it and may calibrated in terms of process variable unit.
Mutual inductance based Transducer
When there are two coils brought in such proximity that the magnetic flux generated due to one current-carrying coil is linked in such a way that an EMF is produced in secondary coil that opposes or resists the change of current flowing through the coil. This phenomenon which affects or changes the current and voltage in a secondary coil is called mutual inductance.
Since we know that a mutual inductance can exist in presence of two or more coils linked with same magnetic field. Here we can derive mutual inductance as shown below-
From the formulas of mutual inductance, it is clear that mutual inductance is a function of self inductance of both the coils- L1, L2 and coefficient of coupling (K). Coefficient of coupling (K) depends on the distance and orientation between two coils and thus measurement of displacement can be performed. And self inductance of coil is again a function of number of turns of coil, reluctance, permeability and geometric factor.
So when a process variable make change into the following factors- such as coils individual self inductance coupling coefficient, it can be measured by detecting change in mutual inductance which can be converted into form of change in voltage in secondary coil or current passing through the coil and may calibrated in terms of process variable unit.
Variable reluctance type Transducer
Since we all know that reluctance for magnetic circuits is basically similar to resistance in electrical circuits which has tendency to oppose change in magnetic flux present in magnetic circuits. It is defined as the ratio of magneto-motive force (or MMF) to magnetic flux (ɸ). Permeance is called as inverse of reluctance which supports to magnetic flux change through magnetic circuits. Other definition for magnetic reluctance (R) is defined as property of magnetic path or core to oppose flux and depends on permeability (µ) and geometry (G) of the core.
As conclusion reluctance of magnetic circuit/ core material is a function of the above given parameters any change in such parameters done by physical quantity such as displacement, force, speed, angular velocity etc. will result change in reluctance which can be measured by combined basic electronic circuitry and can be calibrated as in terms of physical quantity to be measured. Variable reluctance transducers also called as VR Sensor. The sensor detects the change in presence or proximity of ferrous objects. Other than that VR Sensors are used for position, linear velocity, angular velocity, torque, angular speed etc. A simple example of VR sensor is proximity sensor.
Differential transformer –LVDT & RVDT
Another type of inductive transducer is differential transformer which is basically a moving core transformer and produces an electrical output voltage proportional to the displacement of the core attached to the moving object. There are two possible configurations- One for Linear displacement is called as “Linear variable differential transformer or LVDT” and another one is used for angular/ rotary displacement termed as “Rotary variable differential transformer or RVDT”. The LVDT and RVDT both are passive transducers and a type of electro-mechanical transducer. A simple construction of differential transformer is shown as follows-
Click here to read more about-
Linear variable differential transformer or LVDT
Rotary variable differential transformer or RVDT
Self generating type inductance transducers
Electromagnetic Transducer
Electromagnetic transducers are active / self generating inductive transducers in which voltage signal or EMF is induced due to relative motion between a permanent magnet and an iron core/ other Ferro-magnetic material core. It consists of a fixed permanent magnet on which a coil is wounded and an iron core is placed near to magnet so that magnetic flux of permanent magnet can be linked to moving iron core. When there is core movement, the magnetic flux also changes and thus it produces EMF in coil which can be measured. This arrangement is also called as magnetic pick up. The most useful application of electro-magnetic transducer is speed measurement of a rotor shaft where a magnetic pick up is placed near the teeth or rotating gear of shaft and hence speed measurement is performed by calibrating pick up for speed detection with great accuracy. A diagram for electromagnetic transducer/ magnetic pick up is shown below-
Electro-dynamic Transducer (Moving Coil Generator)
Electro-dynamic transducer or a moving coil generator is also self generating active transducer in which a coil is moved within magnetic field produced by permanent magnet and thus it produces EMF across coil and here can be used for velocity. A diagram for moving coil generator transducer is shown as follows-
Eddy current transducer
When a conductor/ conducting plate is placed near a coil carrying alternating current; it induces circular currents within the conductor having its own magnetic field which opposes AC current flow through the coil. The conductive plate that carries circulating current is called eddy current. These circular currents are called as eddy currents. Inducing eddy currents in conductor results in reduction of magnetic flux and hence changes in inductance of coil, which can be detected. The eddy current principle is used for following applications-
- Detection of proximity of the conducting plates using proximity sensor,
- Vibration in rotary equipment such as compressor, pump, turbines etc. using vibration probes,
- Flaw detection / defect measurements in conducting plates/ objects,
- Missing parts finding into final conducting products etc.
Read Also:-
Active transducers
Related Search:-





Paramagnetic Type Oxygen analyzer
Paramagnetic Type Oxygen analyzer
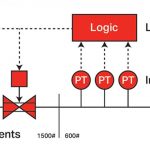
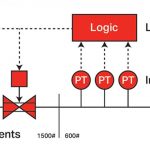
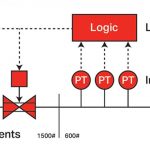
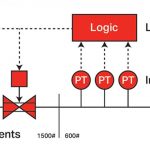
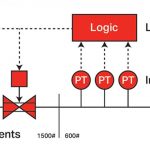
Two out of three (2oo3) Logic
Two out of three (2oo3) Logic





What is source and sink in plants?
What is source and sink in plants?





How sulfur Analyzer works
How sulfur Analyzer works
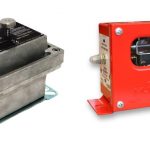
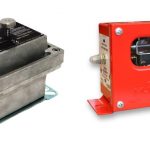
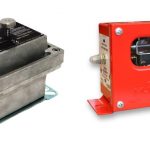
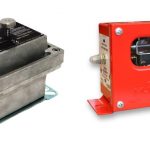
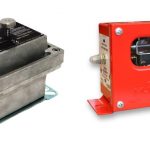
Vibration Switch
Vibration Switch




