Table of Contents
Types of Transducers are having a major role to understand the transducers structure, working, analyzing its output and different conversion and manipulating techniques etc. A broad classification of transducers are given as follows-
- Types of transducers based on Source of Energy requirement-
- Active Transducer
- Passive Transducer
- Types of transducers based on physical phenomenon-
- Primary Transducer
- Secondary Transducer
- Types of transducers based on Its Output-
- Analog Transducer
- Digital Transducer
- Classification based on Transduction Phenomenon-
- Transducer and Inverse Transducer
- Classification based on Construction-
- Mechanical Transducer
- Electrical Transducer
- Optical Transducer
Classification based on Energy Source requirement
Active Transducer
Active transducers are the transducers which do not use any external power for the measurement of process variable. These transducers are self generating devices which operate under the energy conversion principle. In other words, active transducer produces its own equivalent electrical output in response to the physical quantity to be measured. Thermocouples, thermopiles, peizo-electric crystal, photo voltaic cell etc. are some examples of active transducers. Read more….
Passive Transducer
Passive transducers are those transducers in which external power source is required for their operation i.e. for the measurement of process variables, it is necessary to provide external power supply to operate or for the conversion of energy from one form to another. These transducers are also known as externally power driven transducers. Resistive transducers such as RTD, thermistor, strain gauge, inductive transducers such as LVDT, hall sensors etc. are some examples of passive transducers. Read more….
Classification based on physical phenomenon
Primary Transducer
Primary transducers also called as primary sensing elements, are the first and foremost requirement for the measurement and control. The primary transducer is the first element which is directly exposed to the process variable to be measured that senses physical changes or any change in its surrounding and produces an equivalent functional output which is detected by next stage or a second stage. Bourdon tube, diaphragm, bellows in a pressure measurement, bimetallic thermometer, liquid filled thermometer, manometer etc. are some examples of primary transducers.
Secondary Transducer
Secondary transducer is basically a second stage in a measurement system which detects the mechanical or physical change produced by primary sensing element and converts or manipulates into electrical signal mostly. The magnitude of the output signal depends on the input mechanical signal. Some examples of Secondary Transducers are LVDT, Piezo electric crystal, pinion gear arrangement etc.
Classification based on Its Output
Analog Transducer
Analog transducer is the transducer which provides output signal in analog form (of voltage or current) i.e. a continuous function of time in response of input quantity to be measured. Potentiometer, LVDT, thermistor, RTD, thermocouple etc. are some examples of analog transducers.
Digital Transducer
Digital transducer is the transducer which provides output electrical signal in digital form i.e. discrete signal in response of input quantity to be measured. Here Output is in the form of square pulses and having two states (high and low); hence it is called a digital transducer.
Examples- Shaft encoder, limit switch, pressure switch, digital tachometer, digital resolver etc.
Classification based on Transduction Phenomenon
Transducer
When considering transduction phenomenon, transducers are the devices which convert non-electrical physical process variable being measured into electrical signal. These are also called as electrical transducers. Potentiometer, LVDT, thermistor, RTD, thermocouple etc. are some examples of electrical transducers.
Inverse Transducer
Inverse Transducer is defined as a device which is used to convert an electric quantity such as voltage or current into a non- electrical quantity such as displacement, force, pressure, temperature etc. In other words, Inverse transducer is called as output transducer because they convert an electrical signal into non-electrical output. For Examples I to P converter, Piezo electric crystal, Analog Ammeter, The oscilloscope etc. are some inverse transducers.
Classification based on Construction
Mechanical Transducer
Mechanical transducers are a set of primary sensing elements that respond for the change in a physical quantity with a mechanical output such as displacement, force (or torque), pressure and strain. Diaphragm, bellows, manometer, bimetallic strip, flow orifice, pilot tubes etc. are some mechanical transducers.
Electrical Transducer
Electrical Transducer is specified as the sensing device which is used to detect or sense a non electrical physical quantity or magnitude and convert into electrical output signal such as voltage or current proportional to the input being measured. Potentiometer, LVDT, RTD, Thermocouple, Strain Gauge, Piezo-electric crystal etc. are some examples of Electrical Transducer.
Optical Transducer
Optical transducers are based on optical transduction of light signals and rays and utilize optical properties for measurement and analysis. Mostly optical transducers convert light and rays into electrical quantity. So these are also called as opto-electric transducers or photo-electric transducers. Optical transducer uses the property of light such as heat, absorption, adsorption, reflection, emission, radiation and so on.
Read Also:-
Difference between sensor and transducer
Related Search:-
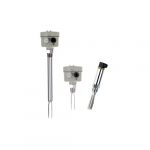
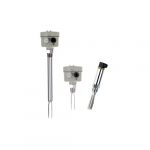
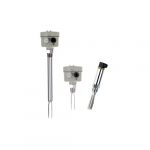
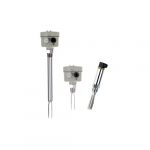
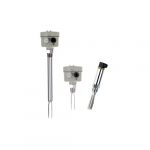
Tuning fork Type Level Switch
Tuning fork Type Level Switch





Displacer/Level Troll Type Level Transmitter
Displacer/Level Troll Type Level Transmitter





Pressure switch calibration
Pressure switch calibration
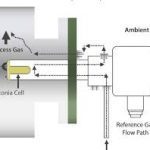
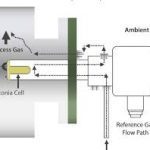
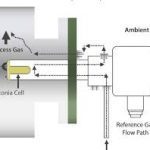
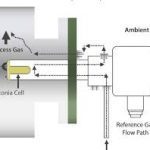
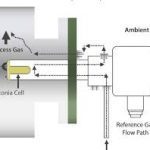
How To Zirconia oxygen analyzer works
How To Zirconia oxygen analyzer works
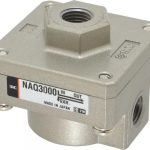
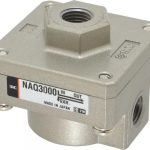
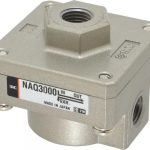
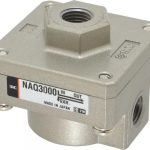
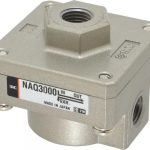
Quick Exhaust Valve
Quick Exhaust Valve
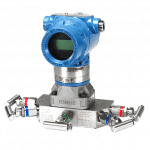
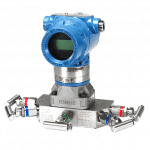
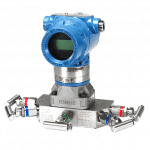
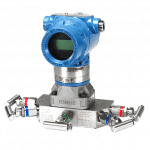
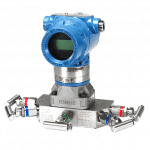