Table of Contents
Control Valve Problems can have several causes. Here we explain the most common reasons.
- Mechanical friction
- Stiction
- Flashing
- Cavitation
- Choked flow
- Hunting
- Valve noise
- Erosion
- Chemical attack
Mechanical friction
A force that tends to oppose the relative motion between two surfaces that are in contact with each other. The friction force is a function of the normal force holding these two surfaces together and the characteristic nature of the two surfaces. Friction has two components: static friction and dynamic friction. Static friction is the force that must be overcome before there is any relative motion between the two surfaces. Once relative movement has begun, dynamic friction is the force that must be overcome to maintain the relative motion. Running or sliding friction are colloquial terms that are sometimes used to describe dynamic friction. Stick/slip or “stiction” are colloquial terms that are sometimes used to describe static friction. Static friction is one of the major causes of dead band in a valve assembly.
Stiction
Resistance to the start of motion usually required to overcome static friction. If a valve with stiction stops moving, it tends to stick in that position. Then additional force is required to overcome the stiction. The controller continues to change its output while the valve continues to stick in position. Additional pressure mounts in the actuator. If enough pressure builds up to overcome the static friction, the valve breaks free. The valve movement quickly absorbs the excess in pressure, and often the valve overshoots its target position. After this, the valve movement stops and the valve sticks in the new position. Stiction might be caused by an over-tight valve stem seal, by sticky valve internals, by an undersized actuator, or a sticky positioner.
Flashing
At the point where the fluid’s velocity is at its highest, the pressure is at its lowest. When the fluid is incompressible (liquid), if the pressure falls below the liquid’s vapour pressure, vapour bubbles form within the valve and collapse into themselves as the pressure increases downstream. This leads to massive shock waves that are noisy and will certainly ruin the equipment. Under such scenario, there are two phases flowing downstream of the valve: liquid and vapour. Flashing cannot be eliminated in the valve if the downstream pressure is less than the vapour pressure of liquid.
If the fluid being throttled by the valve is a liquid (as opposed to a gas or vapour), and its absolute pressure ever falls below the vapour pressure of that substance, the liquid will begin to boil. This phenomenon, when it happens inside a control valve, is called flashing. As the graph shows, the point of lowest pressure inside the valve (called the vena-contracta pressure, or Pvc) is the location where flashing will occur.
Cavitation
Cavitation is similar to flashing in a way that the liquid pressure drops to value below its vapour pressure, causing a liquid to vaporize into vapour bubbles. Both cavitation and flashing occurs because the pressure energy in a fluid is converted to kinetic energy due to the contraction at the valve closure member, causing an increase in velocity. In addition, as the temperature of the liquid increases, the likelihood of cavitation becomes more likely because of the increased vapour pressure. The extent of the cavitation depends mainly on the downstream pressure and the differential pressure across the valve.
If the pressure recovers to a point greater than the vapour pressure of the liquid, the vapour will re-condense back into liquid again. This is called cavitation.
As destructive as flashing is to a control valve, cavitation is worse. The difference is that with the cavitation phenomenon, the liquid pressure increases over its vapour pressure during pressure recovery and turns back into liquid state while during flashing the liquid pressure remains below the vapour pressure throughout.
Choked flow
Both gas and liquid control valves may experience what is generally known as choked flow. Simply put, “choked flow” is a condition where the rate of flow through a valve does not change substantially as downstream pressure is reduced.
In a gas control valve, choking occurs when the velocity of the gas reaches the speed of sound for that gas. This is often referred to as critical or sonic flow. In a liquid control valve, choking occurs with the onset of flashing. The reason sonic velocity is relevant to flow capacity for a control valve has to do with the propagation of pressure changes in fluids.
Hunting
An undesirable oscillation of appreciable magnitude, prolonged after external stimuli disappear. Sometimes called cycling or limit cycle, hunting is evidence of operation at or near the stability limit. In control valve applications, hunting would appear as an oscillation in the loading pressure to the actuator caused by instability in the control system or the valve positioner.
Valve noise
Valve components will tend to vibrate whenever they are subjected to high velocity turbulent flow. Standard control valves will therefore tend to be noisy on high pressure drop applications particularly where flow rates are high, since the low pressure experienced downstream of the seat ring (at the vena contracta) is accompanied by very high velocities reaching as high as the speed of sound.
Erosion
A problem common to control valves used in slurry service (where the process fluid is a liquid containing a substantial quantity of hard, solid particles) is erosion, where the valve trim and body are worn by the passage of solid particles. Another cause of erosion in control valves is wet steam, where steam contains droplets of liquid water propelled at high velocity by the steam flow. Steam may also “cut” other parts of a valve if allowed to leak past. Any fluid with sufficient velocity may cause extensive damage to valve components.
Chemical attack
Corrosive chemicals may attack the metal components of control valves if those components are not carefully selected for the proper service. The effects of corrosion are multiplied when combined with the effects of cavitation. Most metals develop what is known as a passivation / oxidation layer in response to chemical attack. Rust on steel, or aluminium oxide on aluminium, are both common examples that forms due to oxidation of the metal. It results as rapid degradation of the valve components.
Read Also:-
Related Search:-
pH Measurement
pH Measurement





Remote seal DP Transmitter calibration
Remote seal DP Transmitter calibration
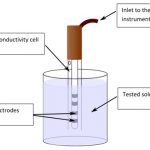
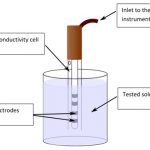
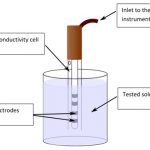
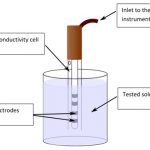
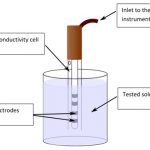
How to Measure Conductivity?
How to Measure Conductivity?
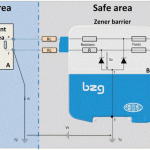
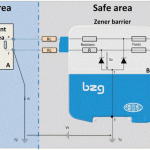
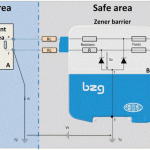
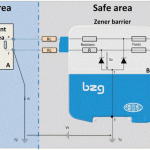
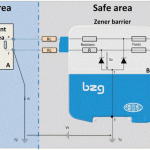
How to choose zener diode barriers?
How to choose zener diode barriers?
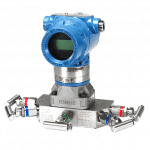
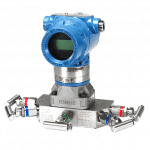
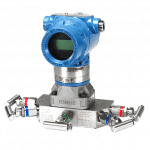
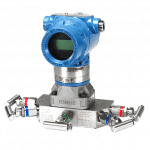
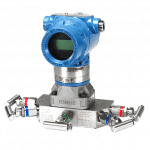
DP transmitter calibration
DP transmitter calibration
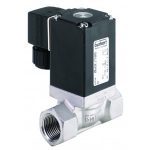
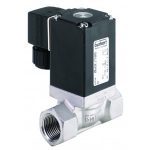
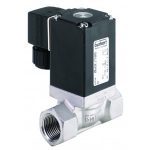
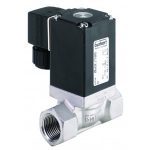
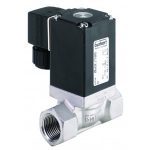