Table of Contents
What is pressure Switch?
Pressure Switch is a Device to monitor process pressure and generate a digital output when a set pressure or set point reached. A bourdon tube, a diaphragm, or a bellows can actuate the switch.
Main parts of Pressure Switch
1. Switching element
2. Set Point Adjusting nut
3. Calibration Scale
4. Piston assembly
5. Pressure range Spring
6. O ring Seal
7. Diaphragm
8. Pressure Ports
How does Pressure Switches work?
Generally Pressure switches consist two contacts (normally open and normally close). If the pressure is below the set point, then contacts will be in a normally open (N.O) condition. Switch will remain open until the pressure increases above the set point. Then the sensing element makes the contact snap to the closed position. The contacts will get back to open condition again if the pressure decreases below the set point.
The contacts in a normally close (N.C) condition, contact will remain closed until the pressure increases above the set point. Then the contact snaps open and will remain open until the pressure decreases below the set point position.
Most pressure switches contains two sets of contacts. One normally open and the other normally close. Thus the switch will work regardless of which kind of contact is needed in a particular installation.
Types of pressure switches
There are many type of pressure switch is given below:-
- Electromechanical Pressure Switches
- Diaphragm Switches
- Bourdon Tube Switches
- Diaphragm Piston (Dia-Seal Piston) Switches
- Piston Switches
- Solid-State Pressure Switches
Electromechanical Pressure Switches:
The most common electromechanical pressure switches are
composed of a sensing element and an electrical snap-action switch. A number of
different types of sensing elements can be used but they have one thing in
common: they move in response to changes in the system pressure. Through their
movement they directly act on the opening and closing of the snap-action
switch’s contacts
Differential pressure switches are slightly different. There are two pressure ports, one for the low pressure side and the other for the high pressure side. The low pressure and high pressure fluids act on the same sensing element. Since the surface areas are equal on each side, the switch is in equilibrium when the pressures are equal. As pressure on the high-pressure side increases, or pressure on the low side decreases, the piston moves up and, at a preset differential pressure, activates the snap switch.
Switches are commonly grouped together based on the type of sensor technology employed. The characteristics of the sensor tend to define the relative accuracy and life one can expect from the switch.
Diaphragm Pressure Switches
use a weld-sealed metal diaphragm which directly acts on a
snap-action switch.
- Pressure up to 10.43 bar and vacuum.
Bourdon tube pressure switches
Bourdon tube pressure switch a weld-sealed bourdon tube is used to actuate the snap-action switch.
- Pressure from 3.45 to 1241.06 bar.
Diaphragm
Piston (Dia-Seal Piston) Switches
Diaphragm piston pressure switch is an elastomeric diaphragm acting on a piston which in turn actuates the snap-action switch.
- Pressure from vacuum to 110.32 psi.
Piston
Switches
Piston Pressure switch is an O-ring sealed piston acts directly on the snap-action
switch.
- Pressure to 827.37 bar.
Solid-State Pressure Switches
In 1980, Barksdale introduced the first solid-state pressure switches. It was a simple device which combined a bonded strain gauge sensor and triac switch. Today, there are a wide variety of solid-state pressure switches that have one to four or more switch points, digital displays, analog and digital outputs, and full programmability.
In many cases they cross the line from being simply a switch to an open-loop controller. In addition to opening or closing the pressure switch circuit(s), they provide a proportional analog 4-20 mA signal or digital output. The analog signal can interface with PLCs (Programmable Logic Controls), DCSs (Distributed Control Systems) and computers. The major advantage lies in cycle life. Solid-state switches routinely have an operational life of 100 million cycles.
Read Also:-
Related Search:-





Float type Level Switch working principle
Float type Level Switch working principle
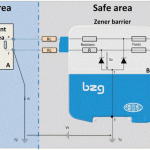
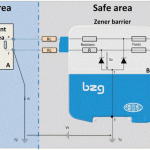
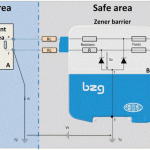
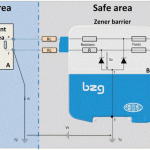
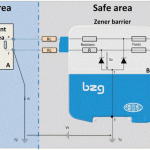
How to choose zener diode barriers?
How to choose zener diode barriers?





Why 4 to 20 mA used?
Why 4 to 20 mA used?





Interview Questions
Interview Questions





Hazardous Area Classifications and Protections
Hazardous Area Classifications and Protections
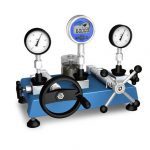
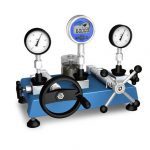
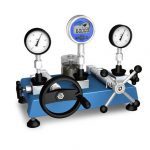
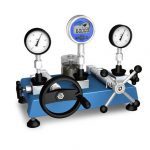
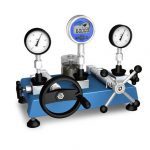