Table of Contents
Displacer level Switch:
This type of level switch uses displacer that do not float on the surface of liquids but suspended on a coil. Displacers are not affected by turbulence or pressure and are
excellent for applications with viscous or dirty liquids. Applications include foaming liquids, heavy oil refineries, paints & varnishes, and chemical plants. To run up to three switching stages, displacers can be set up in combinations of narrow and wide differential. When compared to float-operated switches, displacement controls function at higher pressure conditions.
Displacer Type level Switch working principle
Working principle of the level switch is based on a buoyancy principle. This level switch is consists of Switch Assembly, Wire Rope with Spring Assembly and Displacer suspended on spring. Displacer having more density than the process liquid is used. Spring selection is determined by the weight of the displacer. When level rises it displacer is submerged and amount of weight equal to the weight of process liquid is displaced. This displacement relives spring tension causes the actuation of micro switch.
Types of displacer level switch:
following are the types of displacer level switch
- Single stage displacer level switch
- Dual stage displacer level switch
- Tri stage displacer level switch
Application of Displacer type level switch:
- In Scientific laboratory.
- In Research centres.
- In Chemical industries.
- In Large fuel tanks and sumps, sewage and waste water, interface liquids, petrochemicals, and nuclear power.
- Used when conventional float-operated devices are inoperative.
Difference between Float and Displacer type level switch:
The key differences between floats and displacers are as follows:
Displacer switches are more simpler to test for proper operation than traditional float level switches because they only require the lifting of a suspension, as opposed to the need to fill the tank with liquid all the way to the activation mark with the latter.
In the event of turbulent, surging, frothy, and foamy services, displacement switches are thought to be more stable and dependable than normal float level switches. However, because of their high installation costs and imprecise performance as a result of changes in process density, the employment of displacers is declining in refineries. It has been discovered that float level switches are dependable and practical in various applications.
Displacer settings may be adjusted extremely easily because they can be moved anywhere along the suspension cable. Additionally, these level indicators allow for tank interchangeability. This is because altering the tension of the spring that is attached to the displacers allows for the tolerance of variations in process density.
In contrast to displacers, which can provide a leak path if the torque tube fails, float switches can operate failsafely in harsh process conditions and are available with a glandless design.
A displacer remains either partially or completely submerged in the process liquid, unlike a float, which typically floats above the liquid’s surface.
Read Also:-
Related Search:-
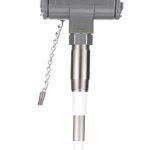
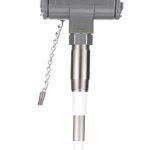
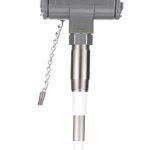
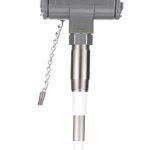
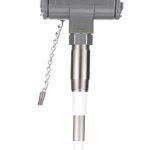
Capacitive level switch
Capacitive level switch
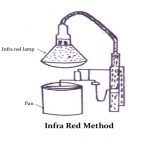
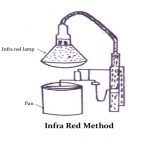
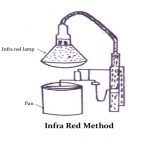
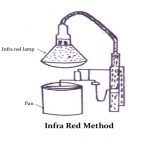
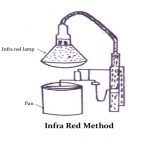
Moisture Measurement
Moisture Measurement
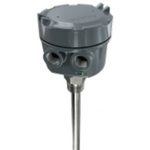
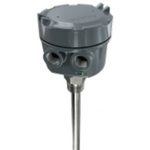
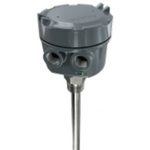
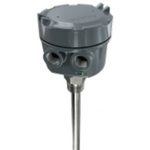
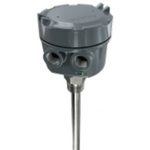
Working principle of vibrating rod Type level Switch
Working principle of vibrating rod Type level Switch
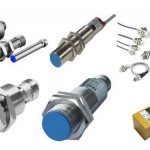
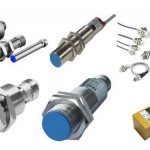
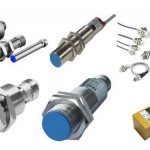
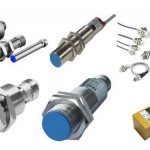
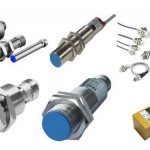
Proximity Switch
Proximity Switch





Process control
Process control
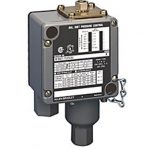
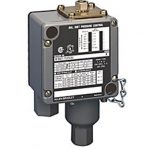
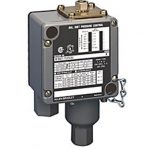
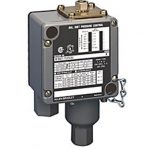
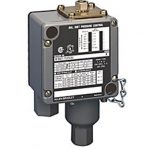